Since the inception of Above Category, we've always stuck to a razor sharp focus on finding the best performing products that rise above marketing hype and truly deliver on giving the best possible experience on the bike. Alongside that focus, we've had an undying fascination with bespoke, handcrafted machines. Throughout our journey, we've come across a number of brands with visions that fall in line rather closely with our own. One such brand is Utah based Enve.
Over the years, Enve has grown to be a household name in the cycling world, known for engineering some of the most premium carbon fiber wheels and cockpit components on the market. From wins in elite Ironman triathlons to downhill mountain bike world championships, Enve has been at the forefront of performance in nearly every niche of the sport. They've also been a brand passionate about custom frame builders, developing the most ubiquitous forks in the market.
Our history with Enve dates back a decade, in the early days of both of our brands. Immediately impressed with their original wheel offerings, we quickly started riding them on our personal bikes and spec'ing them on our client builds. Before long, they even supported our elite NRC team, racing Enve wheels (known as Edge back then) all around the country against the top pros. Over the years, it's been a treat watching the Enve brand grow and their product line expand and evolve.
It should come as no surprise then, that when we were extended an invite to visit their HQ, we jumped at the chance. Enve selected us to be a part of their Builder's Summit—a meeting of the minds in the handbuilt bicycle community, with an in-depth tour of their facilities, ending in a custom bike show during a factory open house. We wanted to give you a glimpse at the inside of this pioneering brand to see just what makes them tick.
Nestled between the Wasatch mountains and the Great Salt Lake, Enve's Ogden, Utah headquarters is quite the sight to behold. It shouldn't be a surprise if the view from their front door strikes you as familiar. That peak in the distance, better know as Mt. Ben Lomond, is the same peak illustrated in the iconic Paramount Pictures logo. It's hard to imagine a more picturesque or idyllic location for a cycling company (or any kind of outdoor company, really) to build its home base. Whether it was by design or coincidence, the new Enve building is surrounded by mountains, trees, and rivers with an endless network of trails straight out the door connecting to it all.
Entering the building is no less impressive than the views outside. The level of thought and design competes with any Silicon Valley tech office. A welcoming open layout, natural light pouring in from every angle, a balanced mix of industrial and organic elements, and cues of the brand's history sprinkled throughout... if you have to work in an office, this is about as delightful as it gets. From engineering, to sales, to creative and marketing, it all happens here.
You'd be hard pressed to find an Enve employee who isn't a die hard cyclist. The parking zones overflow with bikes, all clearly ridden and abused, and all decked out in Enve bits and pieces. Any guesses as to what kind of prototypes or pre-production pieces might be hidden in these bike piles?
As expansive and beautiful as the office side is, we of course can't leave out where the magic happens. Under the same roof lives Enve's manufacturing and production facility. The company holds a lot of pride in this space, producing much of their flagship product right here, in house, and doing the vast majority of it all by hand. When building this facility a couple years back, they had the opportunity to design it all from scratch. Everything about the layout was meticulously thought out to maximize flow, efficiency, and cleanliness.
From start to finish, every single Enve rim is made right here at the hands of skilled workers. Everything starts from rolls of prepreg carbon fiber. The materials get laid up by hand, unique to each model, before getting cut up into kits for pre assembly, and then set into their molds.
Once everything is set up in the mold, they move to the curing phase. As every rim has a unique lay up, they each have a unique curing temperature and time too.
Enve goes to great lengths to ensure rims come out of the mold as perfect as can be. Minimizing clean up not only helps keep manufacturing efficient, but reduces any hazardous waste in the workplace. One of the few robots in the facility is this one here, performing a final fine sanding on the rim edges.
After a final round of QC, it's time to turn parts into a finished, rideable wheel. There's a full fleet of wheel builders getting things laced, tensioned, and finished up to order. Because carpal tunnel is a thing, an operator does use a machine to help with the initial lacing and threading of the spokes. From there, they get passed on to get brought up to tension and trued to perfection. The wheel builder puts the wheel on a hook, where at the other side it's picked up and gets decals applied.
It's not just rims happening here. Carbon fiber stems and hubs get laid up, molded, and finished right here in Utah.
One thing that separates Enve from the rest is how thorough and rigorous their testing process is. Strength, impact, fatigue, compliance, comfort... any new prototypes go though exhaustive stress and performance testing before it goes to market. They bench test nearly all other competitors' products as well, ensuring they know how they stack in the market. They've got a full on machine shop, right in house, which allows them to design and build new test equipment at will, continuously leading to higher and higher standards.
While we got a thorough tour of their test lab, one area that was closed off was the top secret Dark 6 room. Behind those closed doors is where all the special projects happen. There's an endless flow of projects going on, from totally new product ideas to revolutionary manufacturing processes. What specifically are they working on right now? ...that they wouldn't really say.
Clearly, we've been impressed with Enve since the early days and our appreciation has only grown over the years as their product line has improved and expanded. It was all the more inspiring through, getting a chance to see things from the inside and discover just how much care and passion goes into everything the team at Enve does.
Of course, that passion doesn't end there on the production floor. Enve is without a doubt a "built by riders for riders" kind of brand, and their drive for building products comes directly from their quest to push the limits out on the bike. I know, it sounds cheesy, but we got to discover first hand just how demanding of riders everyone at Enve is. Our trip wasn't just about watching sheets of carbon morphing into wheels; we got proper tour of their backyard testing grounds. A brutal, unforgiving, 80+ mile/8k + feet of vertical of mostly chunky gravel, pushing through morning rain into 90º afternoon heat, kind of tour into those Wastach mountains...
... more on that soon.
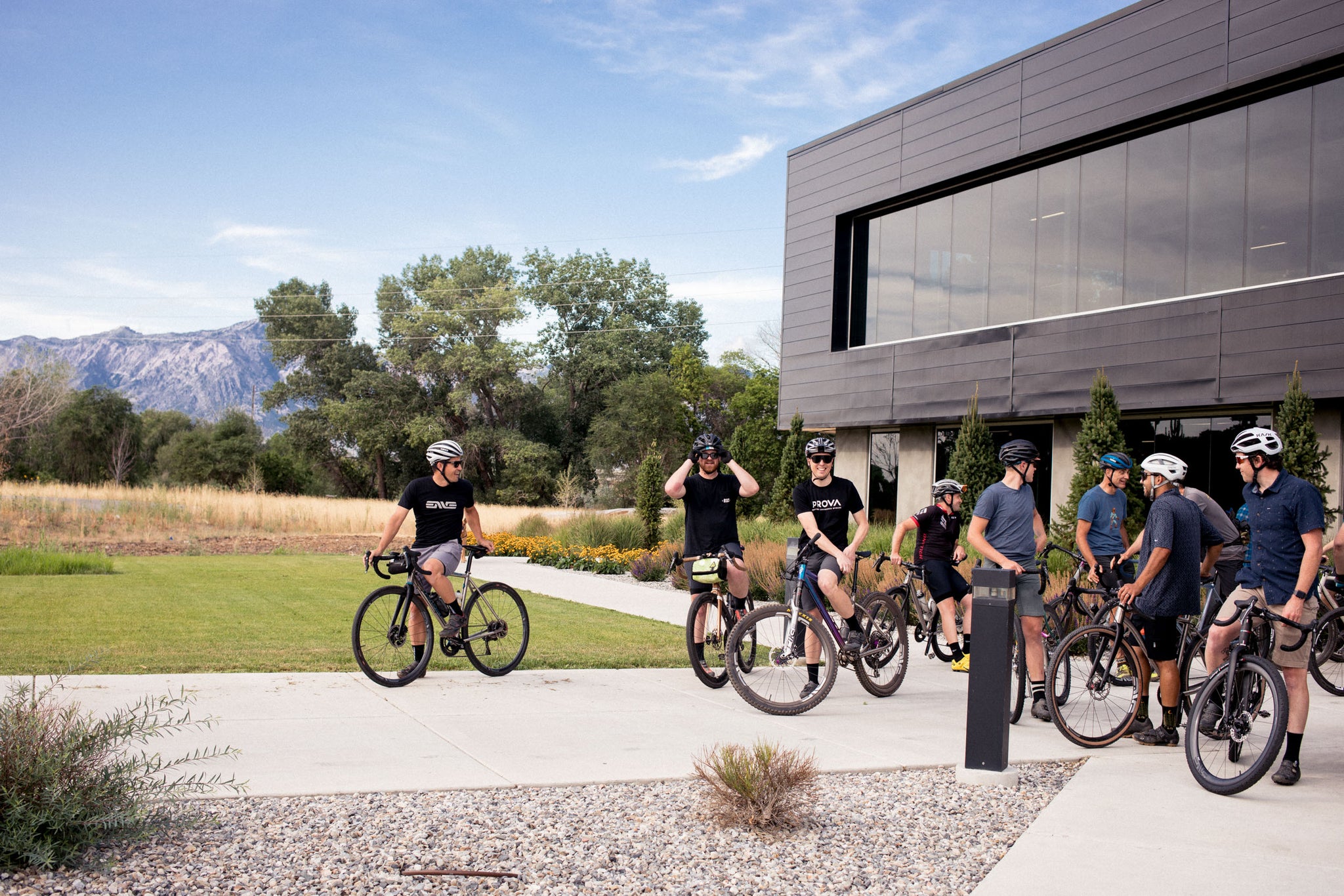
Back to Journal